요즘 가장 핫이슈가 요소수 대란이다. 산업계도 문제지만 특히 경유를 사용하는 차량이 직접적인 피해를 보고 있다. 디젤엔진에서 연소돼 발생하는 질소산화물을 질소와 물로 환원시키는 역할을 요소수가 하지만 요소수 부족사태로 인해 제 역할을 하지 못해 문제가 되는 것으로 신속한 대응 및 장기적으로는 수입처 다변화가 필요해 보인다.
이러한 상황에서 화공을 전공한 공정 엔지니어로서 요소 제조 공정에 대해 관심을 갖게 되었고, 다양한 자료를 검토한 내용을 다음과 같이 정리하였다.

주요 Licensor로는 Stamicarbon(네덜란드, CO2 stripping process, newplant 66% 점유), Saipem S.p.A.(이탈리아, 과거 Snamprogetti에서 변경, NH3 Self-Stripping Process), Urea Casale(스위스), Mitsui Toatsu, Kellogg, Toyo Engineering Corp(독일, 이전의 Yara/Hologies)는 gripping Process),
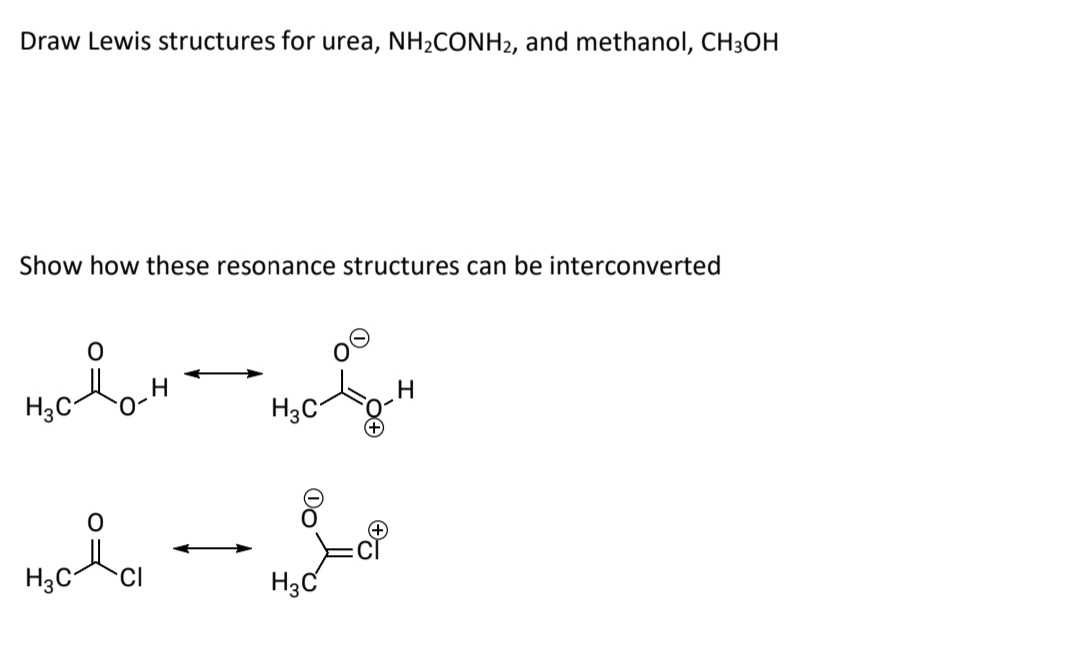
Urea는 100~200bar, 200˚ Cautoclave에서 먼저 ammonium carbamate(NH4COONH2)를 만든 뒤 이는 다시 저압 stripping process에 의해 dehydration이 일어나 urea와 물로 분해된다. 결국 NH3와 CO2의 발열반응을 통해 만들어진 주요 질소비료의 종류로 소사료에도 쓰이고 이온교환수지 등 공업적 목적으로도 쓰이며 최근에는 디젤차에서 발생하는 NOx 배출을 줄이기 위한 SCR 환원제로 쓰인다. Ureaplant는 합성공정과 solidification 공정으로 구성된다. (바람직하지 않은 부반응으로 NH2CONHCONH2인 biuret이 생성되며, 이는 urea2몰이 반응하여 biuret과 NH3로 분해된다.)
실제로 NH3와 CO2 반응시의 양론비는 몰비가 2:1이지만 NH3를 excess로 주입하여(NH3/CO2=2.9~4.1) uera 생성을 촉진시키고 결과적으로 effluent에는 uera, excessNH3, ammonium carbamate, H2O가 존재한다. 따라서 합성 혼합물로부터 urea를 얻기 위해 excess NH3를 분리하고 미반응 중간체인 ammonium carbamate를 분해하여 물을 증발시킨다. 이 urea는 증발공정 후 prilling이나 granulating 처리하여 최종 solid 제품을 만든다.
질소화합물인 Urea는 분자량이 60, 멜팅포인트가 132도이고 비중이 1.335로 물에 잘 녹는다. 주요 용도로는 53%가 고체비료, 31%가 액체비료로 쓰이며 동물사료와 접착제, 수지로도 이용된다.
온도가 증가할수록 Amonium carbamate 분해가 증가하는데 일정 온도 이후에 온도가 증가하면 conversion이 급격히 감소한다. 대기압에서는 반응이 매우 느리지만 100기압 이상이 되면 반응이 급격히 진행되어 전체적으로 부피가 작아지는 반응이어서 고압일수록 정반응이 진행된다. 또한 반응물 농도가 높을수록 정반응이 진행되고 urea 반응이 평형에 도달하는 데 약 20분이 소요되며 conversion을 높이기 위해서는 충분한 시간이 필요하다.
CO2stripping process
1960년대에 Stamicarbon에 의해 처음 도입되었으며 많은 혁신적인 변화를 통해 AVANCORE process로 발전하였으며, stamicarbon의 엔지니어링 파트너인 thysenkrupp에 의해 이 기술을 구현하였다. Poolcondenser는 Utubbundle이 submerged된 수평형 고압 Carbamate condenser로 CO2 stripping 프로세스의 반응기 기능 일부와 falling filmty pecarbamate condenser 기능을 혼합한 것이며, horizontal pool reactor는 고압 컴포넌트를 4개에서 2개로 줄여 ura 합성 공정을 더욱 간소화하였다. CO2 stripping 공정의 특징으로 에너지 소비가 작고 공정 효율이 높아 원단위가 좋고 부식이 낮고 emission이 낮아 공정이 간단하고 유지 관리가 용이하다.
첫 반응이 NH3와 CO2의 빠른 발열 반응을 통해 아모니움카바메이트가 만들어지고, 두 번째 반응이 흡열 반응을 통해 카바메이트가 ura와 물에서 탈수가 진행된다. 최적의 운전조건은 145bar, 180℃이며 N/C(Nitrogen/Carbon) ratio는 3 정도다. 두 번째 반응은 평형 반응이며 반응 혼합물은 CO2로 고압 stripping을 하여 미반응 NH3와 CO2를 제거한다. Strippergas는 pool condenser로 가서 liquid pool 내에서 응축된다. 풀콘덴서는 수평형 vessel이며, submerged Utubbundle이 내부에 있으며, tube 내에서 LP steam이 만들어진다. Conventional type에 비해 pool condenser 방식은 반응기 부피를 30~40% 줄여 투자비를 줄일 수 있다. Exhaustgas는 반응기 탑에서 액체에서 분리된 후 scrubbing을 해 암모니아 emission을 줄인다.
Strippedureasolution 내 NH3와 CO2 농도가 낮아 NH3 recycle은 필요 없고, Solution 내 NH3와 CO2는 저압 reculation stage로 회수된다. Ureasolution은 biuret 생성을 최소화하기 위해 진공 상태로 진행하며 evaporation을 통해 74%에서 96~98.5%까지 농축되어 후단 fluidbed granulation process로 보낸다. evaporation에서 condensate는 desorption을 통해 NH3와 CO2를 stripped하고 ura는 가수분해돼 분리된다. Condensate는 CWmake-up이나 BFW를 위해 polishing 처리하므로 Stamicarbonureaprocess에서 폐수의 발생이 거의 없다.
pool condenser
pool reactor
Granulation Technology
Thysenkrupp는 Yara 비료 기술로부터 fluidbedureagranulation 기술을 구입하여 약 70plant에 적용되며, 특히 uniqueexhaustgaskleaning 기술을 도입하여 친환경 plant를 목표로 하고 있다. 증발공정에서 urea는 formaldehyde와 함께 fluidbed granulation unit으로 도입되어 고순도 solid granule을 만든다. 제품은 냉각된 후 screeningsection으로 lifting 된다. 크기가 큰 물질은 crushing되며 크기가 작은 grain과 함께 granulator로 돌아간다. Widerangesize에서 생산되며 granulator에서 공기로 entrained된 ureadust는 scrubbing system으로 물로 회수한다. 이 물은 증발 및 응축 공정을 통해 make-up하며 환경 측면에서 폐수 발생이 없어 운전의 flexibility와 reliability가 높다.
크기와 고압 아이템 개수를 줄여 투자비를 줄이고 시공 높이를 낮춰 시공비용도 줄이고 열전달효율을 높여 열교환기 크기도 줄일 수 있다. 운전 측면에서 안정적으로 운전이 가능해 load 변화에 민감하지 않다. Duplexsteel을 적용하여 우수한 부식저항성을 나타낸다.
수용액 상태의 ura 용액은 뜨거운 연소가스나 디젤 엔진의 버스에 주입해 우선 CO2와 NH3로 분해된 뒤 NH3는 촉매 존재 하에서 질소산화물과 반응해 무해한 물과 질소로 분해해 NOxemission을 최소화한다.
Ureafluid bed granulation
2~8mm의 granule을 생산하며 입자가 단단하여 dustfree 상태이다. Bulk 이동성과 blending이 우수하며 prilledurea보다 granularurea를 많이 사용한다. 그랜툴은 모빙파트가 없어 유지관리가 용이하고 운전이 용이하며 솔리드핸들링 설비의 개수가 다른 기술에 비해 적어 투자비를 줄일 수 있다.
Ureafluidized bed granulation process
Urea production specification(typical)
Standard size Large size Total nitrogen 46.3 wt% 46.3 wt% Biuret 0.7-0.8 wt% Moisture 0.2 wt% 0.3 wt% Crushing strength 4.1kg (Ø: 3 mm) 10.0kg (Ø: 7 mm) Avage diameter 3.2 mm Size distribution 95 wt% (2-4 mm) Formal dey
액체 암모니아와 가스 상태의 CO2가 반응하여 ura를 생성하는 공정은 크게 1) Synthesis & HP Recovery; 2) MPPurification & Recovery; 3) LPPurification & Recovery, 4) Vacuum Concentration; 5) Condensatetreatment; 6) Prilling의 6가지 섹션으로 구성된다.
SYNTHESIS AND HIGH PRESSURE (HP) RECOVERY
Reactor, stripper, carbamate condenser, ejector로 구성되며 압력은 150bar 정도이며 반응기 내부에는 conversion을 위해 tray가 설치되어 반응기에 주입되는 CO2의 62~64%가 ura로 전환되고 HP section에 따라 85~90%가 전환된다. 이후 Stripper와 Hydrolyzer에서는 MPsteam을 사용하며, 특히 stripper에 주입된 스팀은 Carbamate condenser로부터 회수된다. Plant로서 도입되는 O2는 fresh CO2의 약 0.25 vol% 정도이다. 이 정도의 산소로 equipment passivation을 실시하여 폭발성 분위기를 억제한다.
MEDIUM PRESSURE (MP) PURIFICATION AND RECOVERY
반응물인 NH3와 CO2를 ureasolution에서 부분적으로 strip하여 수중에서 응축시킨 후 그 solution을 반응기에 recycle시킨다. 잉여 암모니아는 운전압력이 17barg인 증류탑에서 분리된 후 별도로 반응기로 recycle된다. 진공운전 preheater shell에서 NH3와 CO2가 부분응축돼 에너지를 회수하는데, ureaton당 steam 200kg을 생산하고 CO2와 passivationair 내에 포함된 CO, H2, CH4의 inert를 washing한다. inert 내에 포함된 암모니아를 제거하기 위해 폭발과 관련된 안전한 조건에서 inert는 천연가스와 같은 flammablegas가 주입된 후 물로 washing되어 암모니아가 제거된 후 inert의 조성이 과량의 flammablegas에 의해 폭발범위를 벗어나도록 한다. Washing된 inertgas는 burner에게 보내진다. 이 섹션은 다양한 NH3/CO2 비율로 운전할 수 있도록 FlexPod에서 오는 ureastream 내 잉여 암모니아는 MP 섹션에서 응축 미회수가 된다.
LOW PRESSURE (LP) PURIFICATION AND RECOVERY
3.5barg에서 NH3와 CO2의 추가 stripping이 일어나고 NH3와 CO2를 포함한 vapor가 응축돼 반응기에 recycle된다. 장기간 shutdown에 대비하여 plant에서 solution을 저장하기 위한 크기의 tank가 설치되므로 plant에서 밖으로 배출되는 solution은 없다.
VACUUM CONCENTRATION
LP section을 진행하는 ureasolution은 70%이며 약간의 NH3와 CO2가 포함되어 있으며 0.3barA와 0.03barA의 2단계 진공을 거쳐 최종 urea 농도 99.8%를 얻을 수 있다. 농축을 위해 필요한 heat는 MPsectione vaporator에서 NH3와 CO2 vapor 부분 응축에 의해 제공된다. 소량의 Moltenurea를 recycle하여 separator의 내부벽을 wetting하여 lumpformation을 방지할 수 있다.
PROCESS CONDENSATE TREATMENT
여기서 에너지 소비를 최소화하기 위해 heat recovery를 실시하고 ura 1 ppm, NH 31 ppm 이하의 프로세스 워터를 만들어 BFW로 재활용한다.
FIINISHING:PRILLING
Moltenurea 99.8%가 55~80mprilling tower 상부에 spraying되고 하부에서 올라오는 공기에 의해 solidification heat를 제거 및 냉각하여 sphere adalure aparticle인 prill을 만들어 별도의 처리없이 저장하거나 bagging한다.
COSTAND UTILITIES OFAN UREA PLANT
2018년 모 엔지니어링에서 아제르바이잔에 설치할 경우 암모니아는 haldor Topsoe가 licensor이고, uera는 stamicarbon이며, 암모니아는 하루 1200t, uera는 2000t을 생산하는 plant로서 하루 25~26MW 전력을 소비한다. Ureaplant는 하루 천연가스 130만m3를 필요로 했으며 프로젝트 비용은 8억유로였다.
Commercial techmology
Introduction
질소 비료의 원료로 대부분 암모니아를 사용하며 생산되는 암모니아의 80% 이상이 요소와 같은 비료 합성에 이용된다. 대부분의 암모니아는 천연가스의 steamreforming과 watergasshift, 그리고 합성가스인 수소와 CO2 분리를 통해 수소는 Haber-Bosch process에서 질소와 반응하여 암모니아를 생성한다. 그러나 중국처럼 천연가스가 부족한 곳에서는 석탄가스화를 통해 암모니아를 합성한다. 2008년 기준으로 암모니아 연 1억 4600만 톤 중 약 27%는 석탄을 원료로 했으며, 중국 내 암모니아 생산 중 97%가 석탄으로 만들었다.
Ammonia and Urea Synthesis
석탄 가스화에 의해 고순도 수소가 생산되고 ASU로부터 추출된 고순도 질소와 반응하여 암모니아를 생성한다.
3H2+N2→2NH3 HH=-23,400Btu/lbmol NH3
반응은 ironbased catalyst 하에서 2,000psi 이상, 370~540℃에서 진행되며, 이 반응은 발열 반응이며, 2~4 단열 촉매층 stage를 통해 연속적인 반응이 이루어지고, 이를 위해 intercooling과 희석이 단 사이에서 진행된다.
Ironbased catalyst 대신 ruthenium catalyst(KBR’s KAAP™catalyst)를 적용하면 10~20배의 activity가 높고 더 낮은 압력에서도 운전이 가능하지만 단점으로 촉매의 deactivation이 상대적으로 빠르게 진행된다. 암모니아 합성 기술의 licensor로는 Haldor Topsoe, KBR/Haliburton, Linde/Lurgi, Uhde가 있다. Acidgasremovalplant나 fluegas에서 캡처한 CO2를 purify 후암모니아와 반응하여 urea를 생성한다.
2NH3+CO2→(NH2)2CO+H2O
Coke-to-Ammonia Block Flow Diagram
암모니아 플랜트의 product인 NH3와 byproduct인 CO2만을 이용해 urea를 만들기 때문에 보통은 NH3 공장과 uera 공장이 함께 있게 된다.
요소는 여러 이름이 있다. Urea, Carbonyldiamide, Carbamide, Carbonyldiamide, Carbonyldiamine, Diaminomethanal, Diaminomethanone으로 불린다.
CH4N2OorCO(NH2)2
CAS : 57-13-6
수중 용해도: 545g/L(at25℃), highlysolubleinwater
용해도: 500g/Lglycerol, 50g/Lethanol, ~4g/Lacetonitrile
pH:13.9
non-flammable, non-toxic
urea는 대부분 농업용 비료에 사용되고 그 밖에 이온교환수지 등에 사용되며 환경설비로 디젤차에 설치된 SCR 내에 주입돼 질소산화물을 질소와 물로 전환하는 데 사용된다. 우선 Urea 용액이 가수분해돼 암모니아를 생성하고, 이 암모니아가 질소산화물과 반응해 촉매반응기 내에서 질소와 물로 환원시킨다. 그 밖에 의료용, 실험실 등에서도 이용되며 동물 사료로도 쓰인다.
천연가스를 이용한 암모니아 생산이 경제성이 있으나 byproduct로서 CO2가 충분히 생성되지 않는 단점이 있다. 최근 fluegas에서 CO2를 회수하는 방법이 적용되면서 CO2 배출도 줄이고 NH3-ureacombination의 stand-alone 질소 비료 complex 설치가 가능해졌다.
두 단계 중 한 단계는 carbamate 형성으로 고온 고압 하에서 액상 암모니아가 기상 CO2와 빠른 발열 반응을 하여 ammonium carbamate H2N-COON H4를 만든다.
2 NH3+CO2 HH2N-COONH4 ( HH=-117kJ/molat 110atm and 160°C)
2단계는 ureaconversion으로서 ammonium carbamate의 느린 흡열반응으로 urea와 물로 분해된다.
H2N-COONH4 ((NH2)2CO+H2O( HH=+15.5kJ/molat160-180°C)
전체적으로는 발열반응이며 첫 번째 반응열이 두 번째 반응을 유도한다. Urea 전환이 완벽하지 않아 미반응인 Ammonium carbamate에서 urea는 분리돼야 했고 초기에는 압력을 떨어뜨려 carbamate를 NH3와 CO2로 분해해 분리했지만 recycle을 위해 재압축하는 것은 비경제적이었다. 토탈리사이클 대신 stripping concept를 적용해 프로세스를 단순화하고 열회수를 통해 프로세스 재사용이 가능해졌다.
2 NH2CONH2 → H2NCONHCONH2+NH3
위부반응인 biuret 생성은 농작물에 toxic해 NH3를 excess에 주입함으로써 피할 수 있다.
부식 측면
Ammonium carbamate는 금속에 부식성이 강하지만 약간의 산소를 연속적으로 주입해 SUS 표면에 passiveoxidelayer를 유지해 부식을 최소화할 수 있다. Duplex를 사용할 경우 산소 없이 운전이 가능하다. Saipem은 zirconium과 titanium을 사용한다.
Finishing
Urea는 prill, granule, pellet, crystal, 그리고 solution에서 생산된다. Prilling 방법을 통해 보다 경제적으로 생산할 수 있지만 granul에 비해 강도가 약하다.
Effluent는 우선 NH3를 stripping한 뒤 Solution은 일련의 감압 과정을 거쳐 분해가 일어난다. 미반응 Carbamate는 NH3와 CO2로 분해된 후 반응기로 recycle된다. Ureasolution은 증발과 결정화를 통해 농축되고 결정은 다시 prill과 granul 형태의 urea를 만들기 위해 melting된다.
Description of flow sheet:
액체 암모니아를 pumping하고 기체 CO2를 압축하여 반응기로 보낸다. Urea 합성 반응기 내부는 부식으로부터 보호하기 위해 oxide film으로 lining되어 있으며, autoclave 내에는 촉매층이 존재하며 180~200 기압과 180~200도에서 운전된다. Plugflow 형태로 진행되며 moltenurea는 탑에서 제거된다. 이후 고압 슬러리는 1기압에서 flashing되어 excess NH3를 제거하고 분해된 Amonium carbamesalt는 recycle된다. Slurry는 vacuumevaporator로 보내져 농축된다. Slurryurea가 prilling tower top에 들어가 spray되고 아래에서 올라오는 공기로 건조 및 냉각이 진행된다. 이 과정에서 증발한 수분은 탑에서 제거되고 ura는 건조해 bottom에서 제품을 얻는다.
Biuret Formation:
2 NH2CONH2 ——————————————————————————
urea 내 1% 이내로 유지해야 한다. 체류시간이 길거나 온도가 높거나 물의 양이 적을 경우 biuret이 생성된다.
Reactor effluent:
약간의 inert와 기상 상태 반응물이 포함된 2phase fluent는 HP stripper로 가고 첫 번째 carbamate가 분해된다. 대부분의 inertvapor는 MPsection의 carbamaterecycle과 함께 carbamate condenser로 가고, carbamate separator로부터 분리된 carbamate는 반응기에 재주입되고, inert는 MPdecomposer로 간다.
H.P. Stripper:
falling film type heatexchanger이고 tube 위에는 pallringbed가 있고 그 위에 sievetray가 있다. Tube는 titanium이고 shellside fluid는 MPsteam이다. 145barg로 운전하는 stripper에 effluent가 유입되고 packingbed 상부에서 distribution 및 heat-up된다. 그래서 CO2는 암모니아의 stripping에 의해서 solution 내에서 그 양이 줄어든다. Carbamate 분해열은 shell의 MPsteam에 의해 제공된다. 분해는 증발된 과잉 NH3의 가열 및 CO2 stripping에 의해 진행되며 NH3 richgas는 위로 올라가면서 CO2를 제거하고 하부에는 농축된 ureasolution이 purification으로 보내진다. Striper Overheadvapor는 180barg에서 가압되어 예열되고, carbamate condensertubeside에 들어가고, shellside에서 LPsteam을 생산하면서 carbamate는 응축된다. 이 condensate는 carbamateseparator로 가고, solution은 ejector에 의해 반응기에 recycle하며, 약간의 NH3와 CO2를 포함하는 inertgas는 MPdecomposer로 간다.
UREA PURIFICATION:
3단으로 압력을 낮춤으로써 ura 정화가 일어난다. 즉, 18barg, 4.5barg, 0.35barg의 순차적으로 감압한다. Ureapurification이 일어나는 열교환기를 decomposer라고 한다. MPinert washing tower 상부는 3개의 valvetray로 구성되며, 물로 inertgas를 scrubbing하여 암모니아가 제거된 inert 가스는 ventstack으로 보내진다.
대기배출가스 폭발성 분위기 방지
반응기에 들어가는 CO2에는 N2, Ar 외에 H2, CH4, CO의 소량이 포함되어 MPinert washing tower에서 대기vent 시 폭발성 분위기를 형성할 수 있다. Saipem 프로세스의 passivationair량이 매우 작아 큰 문제가 되지 않는다.
UREA CONCENTRATION:
Prilling을 하기 전에 ura를 99.8%로 농축하고 이를 위해 수분을 제거하기 위해 진공 상태에서 가열한다.
UREA PURIFICATION at M.P.Decomposer:
3개의 part로 나뉜 falling film heatexchanger다. 탑 세퍼레이터에서는 flashgas가 분리되고, middled composer에서는 carbamate 분해가 일어나며, bottomholder에서는 약간의 inert가 함유된 농축ura가 저장돼 LP decomposer로 보내진다. 쉘사이드 MPsteam에 의해 분해열이 제공되며 17barg, 157도에서 분해가 진행된다.
나머지 CO2가 거의 없는 Solution이 stripper bottom에서 나와 18barg로 팽창하고 MPdecomposer 탑에 들어가고, Solution이 tubbundle에 들어가기 전에 flashgas가 제거된다. Solution의 falling film distribution은 ferrule에 의해 진행되며 separator 탑을 나오는 NH3, CO2richgas는 vacuum pre-concentrator에 가서 부분적으로 ureapript에서 온 수용액 상태의 carbamesolution에 흡수된다. 가스의 흡수와 응축을 통해 ureasolution에서 수분을 증발시켜 흡수열과 응축열을 제거하므로 evaporation stage에서의 LP steam을 save할 수 있다. 이후 가스는 MPcondenser로 가고 CW에 의해 가스의 잔여 흡수열과 응축열이 제거된다. CO2가 거의 흡수되면서 MPcondenser의 mixture는 MPabsorber로 간다.
M.P. Absorber:
bubblecaptray가 설치된 column이며 bottom에 sparger가 설치되어 CO2 흡수와 NH3rectification을 수행한다. RefluxNH3가 absorbertoptray에 들어가고 MPinert washing tower에서 오는 수용액 암모니아 용액이 3단으로 들어가 tray washing을 한다.
MPcondenser에서 오는 twophase NH3, CO2, H2O는 columnbottom으로 들어가고 sparger에 의해 carbamesolution이 distribution된다. 미응축 NH3, CO2, H2O 및 인ertgas는 차가운 refluxNH3에 의해 상부에서 흡수되고 대부분의 CO2, H2O는 Amonium carbamate로 응축되어 bottom으로 내려간다. 응축열은 암모니아 증발에 의해 제거되고, 인버트 가스는 NH3에 포화되어 absorber 탑을 나오며, Amoniacondenser에서 CW에 의해 암모니아가 부분 응축되어 Amoniareceiver로 들어간다. Bottom solution은 ura 합성 반응기에서 recycle 된다.
Ammonia Receiver:
inert가 포함된 나머지 암모니아 가스는 inert washing tower인 MPfalling filmabsorber로 가서 위에서 내려오는 물에 의해 암모니아 가스가 흡수된다. 흡수열은 CW에 의해 제거되고 이를 위해 absorberbottom의 water-NH3 solution을 recirculation시키면서 냉각시킨다. 2.5barg로 운전하는 tower로 feeding하기 전에 condensate는 tower에서 나오는 puried condensate에 의해 예열된다. Solution이 ura에 오염되어 있기 때문에 고온 저압하에서 가수분해된다.
NH2CONH2+H2O———>2NH3+CO2+Heat
UREA PRILLING : PRILL TOWER :
높이가 약 100m인 tower로서 톱에는 prill section이 있고 bottom에는 scraper가 있다. Moltenurea가 펌프에 의해 prilling tower 상부의 회전하는 bucket으로 들어가고 hole을 통해 나온 ureadrop은 아래로 떨어지면서 자연 대류에 의해 위로 올라오는 공기에 의해 urea 냉각 및 solidification된다. prillingurea는 rotary scraper에 의해 beltconveyor로 이송되어 weighing machine이나 저장 혹은 bagging으로 보내진다.
DEDUSTING SYSTEM:
prilling tower 상부를 나오는 스트림에는 ureafinedust와 암모니아가 섞여 있다. 분진의 방출을 방지하기 위해 데드 usting을 실시한다. 최대 대기배출 허용치는 30mg/Nm3air이다.이를 위해 다단 스프립을 수행하고 demister 상부에서 spraying water를 통해 ureafine을 녹여 제거한다.